The Intricacies of Proper Duct Installation
Ducts work to distribute air conditioning to using heating, ventilation and air conditioning (HVAC) systems throughout the building. If they are not properly designed or installed, the consequences can be costly and potentially dangerous to health. Leaking ducts can lead to poor indoor air quality (IAQ). Indeed, "In recent years, comparative risk studies conducted by the EPA and its Science Advisory Board (SAB) have consistently ranked indoor air pollution among the top five environmental risks to public health" (epa .gov).
In addition to IAQ issues, improperly installed ductwork can lead to wasted energy, excessive wear and tear on the HVAC system, and increased inconvenience to building occupants.
Ductwork includes return air transfer, supply and exhaust systems:
· Return: Transfers air to the HVAC system to condition it.
Power: Distributes conditioned air throughout the building.
Exhaust: Provides system ventilation.
Supply, return, and exhaust ductwork have common and product-specific considerations that are often overlooked during installation.
A significant portion of duct airflow problems result from misinterpretation or ignoring of applicable manufacturer codes, standards, or specifications as they apply to duct integration in duct systems. The purpose of this article is to educate you and help prevent some of the most common design and field installation discrepancies observed by our field inspectors. These include:
· Tight bends and crimping around neighboring materials of construction in an attempt to reach component connections.
· Excessive length of conduit.
· Fixing and sealing of ducts to connections to components.
| setting up the system. Often our inspectors will observe that electrical contractors are responsible for installing the exhaust fan and enclosure in their field of work due to the fact that fans are an electrical device. Most electricians are not well trained in air flow requirements or exhaust duct installation requirements. Our inspectors have also observed other traffic damaging the ducts or impairing the airflow capacity while building other systems around the ducts.
1. Tight bends and crimps
Air conditioning and exhaust ducts suffer from a common installation problem: reduced duct airflow in ducted systems flexible. Two of the most common offenders are closely related: sharp turns at changes of direction and crimping conduit to other commercial components. Bends in the duct should be gradual to avoid loss of airflow due to turbulence created as a result of the sudden change in direction.
Interruption of airflow at elbows in attic space openings typically occurs when abrupt 90 degree changes in direction are installed or when there is only a single support, usually positioned at the elbow itself.
Other times this can occur when a straight bellows connection collar (defined as the passage between the inner core of the duct and the damper) is used instead of a 45 connection collar or 90 degrees integrated into the bellows. areas such as terminations near the shallow attic at the end of a wall. This has the potential to significantly reduce airflow when it terminates at the damper. Once the wire helix (see Figure 1) supporting the conduit is compromised or bent, the crimp condition will worsen over time as the wire yields to gravity. The following photos illustrate these typical and incorrect conditions:
The conduit shown in Exhibit 3 (right) was a 10 inch radius conduit, but the top blown insulation compressed the conduit to less than 7 inches when approaching the boot. This "throttling" the airflow, as well as creating turbulence due to the change in shape of the duct, further reducing the actual airflow.
A viable remedy, although slightly less "designed by value", is to change the style of the boot or provide a sheet metal elbow to accommodate the confines of confined spaces maximizing the airflow of the duct and cabinet to save, as shown in the following examples:
Other examples of tight bends caused by improper installation and incorrectly selected components are shown below:
Industry Solutions for Curves
The Air Duct Council (ADC), formerly known as the Air Diffusion Council, is a recognized organization for HVAC industry standards for the diffusion of installation details flexible ducts and performance measures for efficiency and quality (regularly referenced by government agencies, architects, engineers, fabricators and HVAC contractors). With respect to bends, the diameter changes often resulting in diligence in identifying the diameter at each bend by the installer. CDA recommends a diameter no narrower than conduit for the elbows, with supports before and after the elbows (see Appendix 8, below). This practice will reduce the problem of pressure drop caused by constriction and turbulence, as well as improve airflow.
The Air Conditioning Contractors of America (ACCA) is another standards association that creates standards for the design, maintenance, installation, testing, and performance of indoor environmental systems.
The following illustration shows an excerpt from the ACCA friction understanding diagram, where a steep, tight curve creates excessive turbulence, which affects airflow capacity beyond that point:
Bends to exhaust pipes
Supply and return pipes aren't the only pipes that can experience pressure drops from tight bends and crimping. Exhaust ductwork is governed by the same airflow principles as air conditioning ductwork in the ADC guidelines and has the same problems resulting from improper installation. A common misconception is that the exhaust fan "can handle" the pressure loss created when sharp turns are made immediately after exiting the ventilation unit. This does not take into account the resulting turbulence which requires excessive pressure to fully open the return valve (device which allows airflow in one direction and prevents reverse airflow) and therefore further reduces the regulated stroke length. Additionally, exhaust fan units are often installed opposite the external vent termination, creating unnecessary bends (and length), which we will discuss later in this article.
As mentioned earlier in this article, improper installation of exhaust fans and duct connections is often the result of the electrical contractor being responsible for installing the exhaust fan and enclosure into the frame. of his work since fans are an electrical device. While the general position of the fan can often be checked on floors, the direction of the fan outlet usually cannot (unless specified in mechanical plans).
In addition to the industry standards listed thus far, most waste handling equipment manufacturers have their own duct installation methods that meet or exceed the standards of the industry. For example, Broan® and NuTone® specify in the Correct Ducting Guide to optimize exhaust fan performance: “Orient the fan housing so that the fan outlet points in the direction of the outlet point. The most crucial part of the funnel is the first 24 inches out of the case, there should be no bends in this initial funnel.
"Unfortunately, the desire to deliver a finished product on time often prevents you from spending time reading the instructions and guidelines provided by specific manufacturers. The following photos illustrate an example of poor installation practices and Excerpts from Guide to Correcting Conduit:
Crimping
Crimping occurs when conduit is bent or otherwise distorted by commercial components such as frames, plumbing, electrical equipment, and even electrical conduit. Sheet metal HVAC This not only obstructs flow and increases friction, but often impairs the ability of the inner core of the duct to retain its shape integrity by bending flat or twisting the wire (helix) that maintains the circular shape This will further permanently reduce the airflow capacity of the duct for a period of years before loss of flow is evident. on avoiding crimping in its guidelines: "Conduit should not be crimped against joists or joists, pipes, wires, etc.
as it increases pressure drop and reduces air flow." as seen below:
The photos below show some examples of crimping, which can greatly reduce flow of air delivered from the ducts to the damper:
Proper planning of the layout and positioning of the trunk and the branch duct in the floors both in the mechanical design phase and in the installation phase is recommended to avoid crimping conduits) that are installed in floor joist spans and in wall grooves It is strongly recommended to verify isometric details in plans for locations of HVAC, plumbing, electrical components and structural members impenetrable and compare them to ensure adequate space and paths for all components It may be necessary to alter the position and/or increase the depth. saints.
Joist boxes provide limited space for integrating multiple components, including other conduit, and can create significant crimping issues, as shown in the photo below:
2. Length Excessive
Another common occurrence that increases friction and reduces airflow is the installation of excessive length of flexible duct in air conditioning and exhaust systems. The duct length should be long enough to supply conditioned air to the specific location or room, or exhaust exhaust air to the outside as soon as possible. Longer ducts may increase the size of air handler needed to deliver the same cubic feet per minute (cfm), or the HVAC system may not be able to deliver the designed cfm in all locations. Excessively long supply ducts were once commonly used to place logs in places where the greatest conductive exchange of heat energy with the outdoors occurs, usually near single-glazed windows and doors.
These penetrations at exterior wall points lacked the insulating qualities typical of modern components and recommended installation techniques. For supply and return ducts, the recommended practice in the HVAC industry is to have short branch ducts from one or more centrally located main ducts. The Environmental Protection Agency (EPA) states in their Energy Star® Right-Sized/Compact Ductwork: "The primary objective of ductwork design is to provide adequate air distribution throughout the residence. To achieve this efficiently. From an energy point of view, the ductwork should be sized and arranged to facilitate airflow and minimize friction, turbulence, and heat loss and gain. The optimal air distribution system has "right-sized" ducts, minimal runs, the smoothest possible internal surfaces, and the fewest changes in direction and size.
”
Not only do unnecessarily long runs reduce airflow due to the increased length, but installers often do not fully extend when pulling these stretched runs (stretched or strained), which creates longitudinal compression and causes loss of airflow due to friction. This compression of the duct increases the friction rate by 2 to 4 times according to the ADC, as noted below:
The ADC further states: "Properly consider the length of the duct, the losses bend, failure expectations, or routing As not all flexible duct is the same, use the flexible duct manufacturer's air friction loss data to size ducts if possible. the generic table of friction losses in flexible conduit in the ACCA D Handbook Quite often, excess sheathing results in a "snake"; a combination of excessive bends and length of sheathing, which greatly increases the "equivalent" length of the regulated sheath.
This often occurs due to the duct running around obstructions and the installer's inability to remove excess material, especially when pre-cut lengths are supplied by the HVAC contractor to their own installers , as shown in the example below:
3. Fastening and Sealing
Another overlooked and often misunderstood part of installing flexible duct is fastening and sealing . Current and previous revisions of the Uniform Mechanical Code (UMC) and International Mechanical Code (IMC) state that fasteners and sealing components must "conform to UL 181 and must be installed in accordance with Sheet Metal and Air Conditioning Contractor's National Association (SMACNA) - HVAC-Metal and Flexible Duct Construction Standards".
Sealant components listed in UL 181A and B/FX should be labeled on the tape at intervals up to to 6" if putty, be labeled on the container. UL Certified tape has the good adhesion and exceptional shear strength needed to stay in place effectively throughout the life of the HVAC system.
However, it is not uncommon to see some HVAC contractors attempt to cut their financial costs due to the rising cost of UL listed strips. In the example below, the cost difference was the reason the unlisted tape was applied:
Fasteners for flexible and non-metallic conduit should be installed by grouting and then mechanically fastened with a band, as specified by SMACNA in subsection S3 .33, which states: "Nonmetallic flexible conduit must be attached to the sleeve or collar with a rubber band. If the conduit collar exceeds 12" (305 mm) in diameter , the tie should be placed behind a stub on the metal collar." These bands are best secured in place with a nylon tie tension tool.
| Additionally, flexible exhaust ducting often remains unsecured or loosely secured by a single screw, despite being governed by the same codes and guidelines as the supply and return ducting industry. Air conditioning ducts and exhaust ducts that are not properly sealed or secured can eventually have leaking issues.
These issues, already present at an early stage of rough construction, may not become evident during duct and hood sandblasting tests at dampers and exhausts in the final stage of construction - except in the most extreme cases. serious. Providing exhaust and conditioning airflow through oversized mechanical components may allow an acceptable initial test window, but failures may occur years later.
The duct will continue to collapse at those points where the structural stability of the duct shape was initially compromised and in combination with reduced airflow due to aging mechanical equipment, as well as inefficient connections who separated and fled. A third-party quality assurance program could easily identify such issues for the builder.
Conclusion
Rely solely on the skills and knowledge of your operations or the representatives of your local jurisdiction to assess these conditions and each of the component connection and intersection is not realistic. Although the commercial contractors you hire are knowledgeable, most do not check every installation of their employees with internal quality control. Building services are only responsible for providing observations based on minimum code compliance for a very small sample.
Earth care contractors offer top rated 24/7/365 local service at no extra cost. Visit us as https://www.earthcarebrands.com/ To learn more
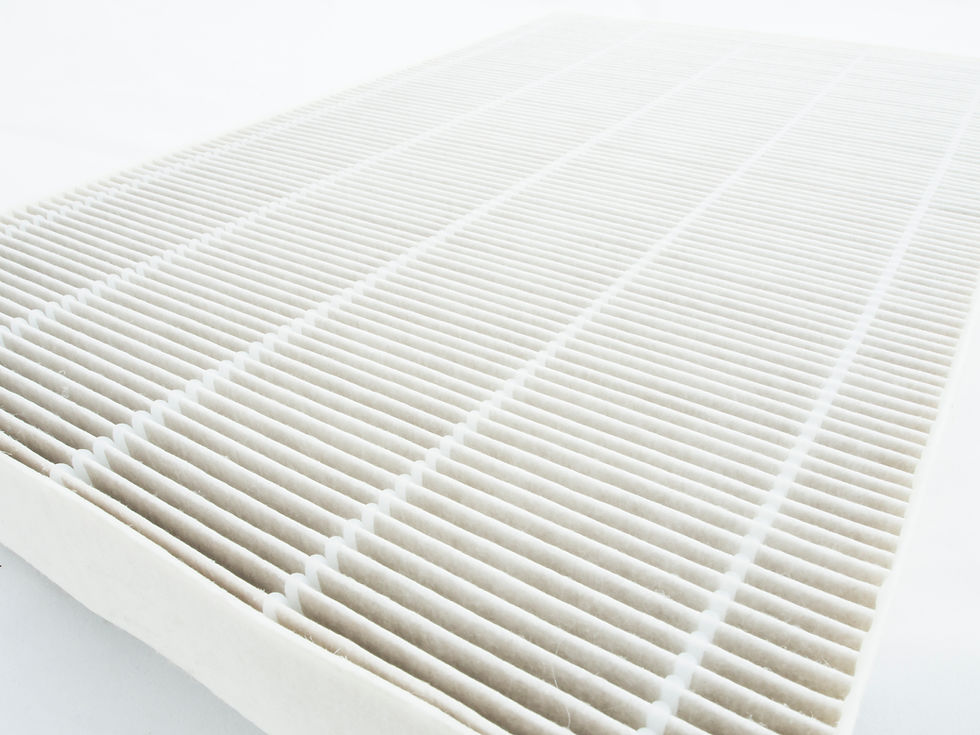
Earth care contractors offer top rated 24/7/365 local service at no extra cost. Visit us as https://www.earthcarebrands.com/ To learn more
Comments